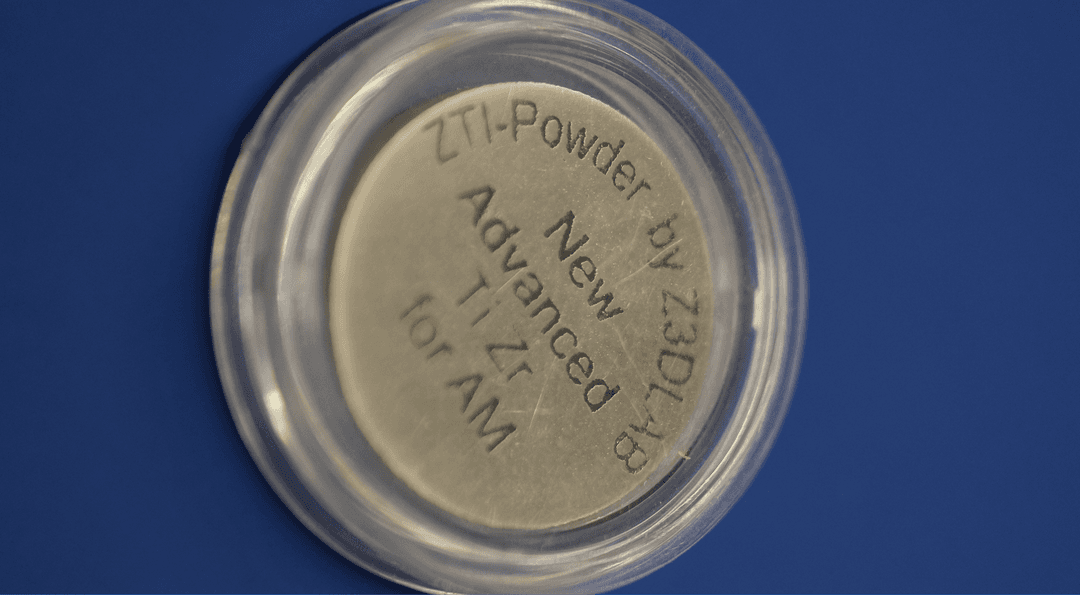
Z3DLAB
Partner Company
Z3DLAB is a technology company focused on materials science, specializing in high-performance titanium powders for additive manufacturing applications, particularly in metal powder production and the fabrication of high-value-added parts, targeting the aerospace and medical sectors.
The company’s flagship product is spherical titanium powder, with an average market price of around €250/kg. Currently, the powders produced by Z3DLAB are priced at approximately €400/kg after production. The goal is to reduce these costs using its A3P Circular process, aiming to bring the price down to around €100/kg. A technical feasibility trial began in September 2021, initially producing ZTM14N powder. Although the powder is currently available in small quantities, the first additive fusion took place in December 2021, allowing the first analyses to be carried out. To move forward, the overall project requires a long-term partnership with LSPM to develop the powder manufacturing technology and optimize fusion parameters. Z3DLAB’s primary market is the sale of advanced materials for additive manufacturing (AM) and the licensing of Z3DLAB applications. The company is based in France and has established connections with the French aerospace sector by becoming a member of the ASTech competitiveness cluster, which is dedicated to aerospace. Z3DLAB has also forged partnerships with French academic institutions such as CNRS, CEA, and LSPM. The company has a scientific committee composed of metallurgists and medical experts, reflecting its commitment to diverse fields.
The company has developed several powder blends divided into two families: ZTi-Powder® (including ZTP10 and ZTP20Z powders) and ZTi-Med® (which includes ZTM14N powder).
Z3DLAB has been recognized as a company in the Breakthrough Technologies (DeepTech) program, demonstrating its commitment to advanced research and technological development. It has also received a grant of €1 million.
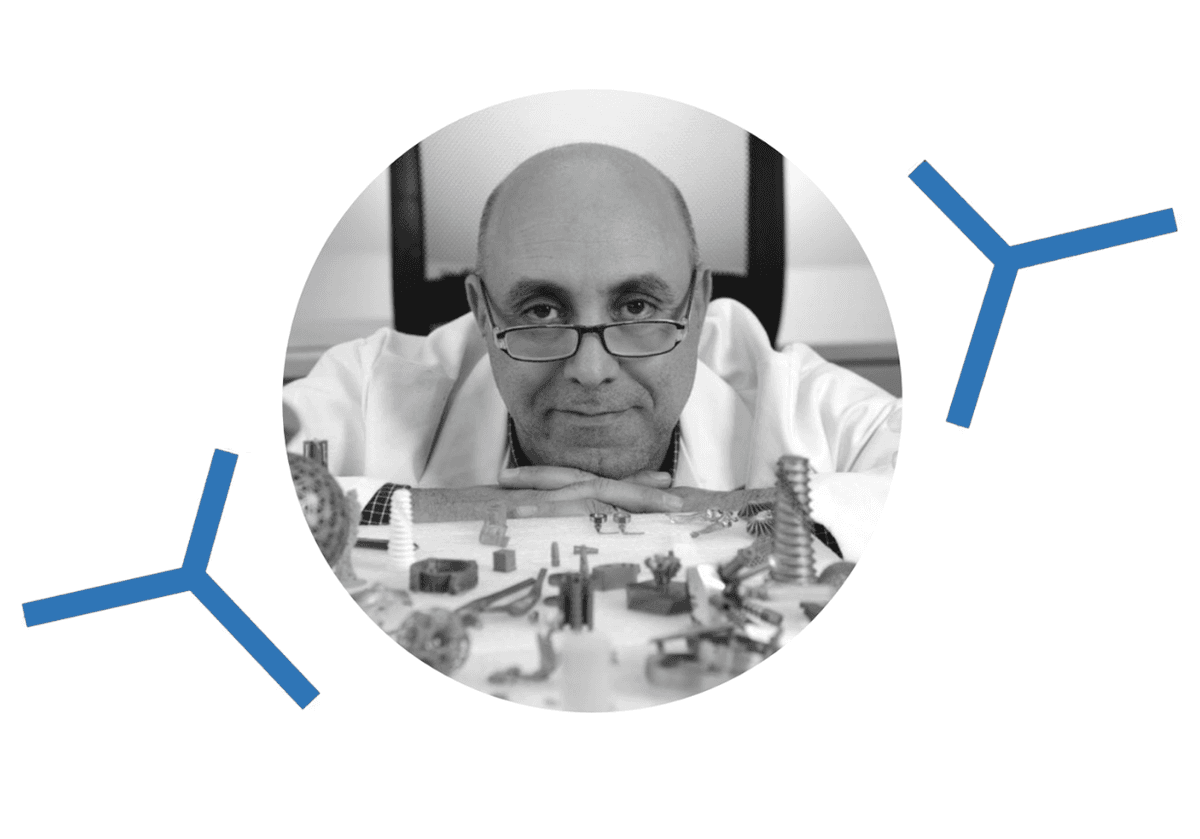
Madjid Djemai, President of Z3DLAB, is a computer engineer, inventor, and former Research and Development director. He founded Z3DLAB in 2014, along with his two partners, specializing in additive manufacturing through metal powder bed fusion.
After nearly two years dedicated to R&D, the company currently holds four patents, enabling it to enter the global markets of aerospace, medical, and energy industries. Z3DLAB develops its own powders and manufacturing processes. The company gained recognition with the launch of ZTi-Powder®, a titanium/zirconium composite material, the hardest material in the world for additive manufacturing via laser fusion. Furthermore, in December 2016, Z3DLAB and HS HI-TECH, a Korean expert in semiconductors, signed a joint venture: Z3DFAB. They leveraged their combined expertise to create the first Digital Additive Manufacturing production center in Korea.
Thanks to its partnership with the Paris 13 University and the AVRILE association, Z3DLAB benefited from collaboration with a CNRS laboratory for the development of new powders and regular expertise in their R&D. Z3DLAB also received support from Val d’Oise Technopole, an association that helps businesses in the nursery with their development, providing simplified connections and support with funding actors (Bpifrance, Region IDF, Scientipole Initiative, COFACE).
LSPM/CNRS
Scientific Manager and Name of the Academic Laboratory
The LSPM (Laboratoire des Sciences des Procédés et des Matériaux) is a CNRS research unit with approximately 130 staff members, including over 30 PhD students, 61 researchers or faculty members, and 20 technicians and administrative staff. Its research is multidisciplinary and covers a wide range of topics in process science and materials, from the design of materials of all types, the development of manufacturing processes, to the study of the structure and constitution of materials at all scales, and the analysis of their behavior (macroscopic) and the mechanisms driving it. The laboratory also develops strong multi-scale modeling activities of material behavior, structures, and processes under different environments.
The LabCom proposal is led by the 2MP team (Physical Metallurgy, Microstructures, Properties) within the MECAMETA thematic axis (Mechanics, Metallurgy). The 2MP team has access to the CARAMEL platform (the SÉSAME project co-funded by CNRS and the Île-de-France Region), hosted by the LSPM, which includes, among other equipment, a GLEEBLE physical simulator and a hot isostatic pressing machine (both unique in the academic field), as well as innovative equipment for microstructural characterization and macroscopic mechanical behavior study.
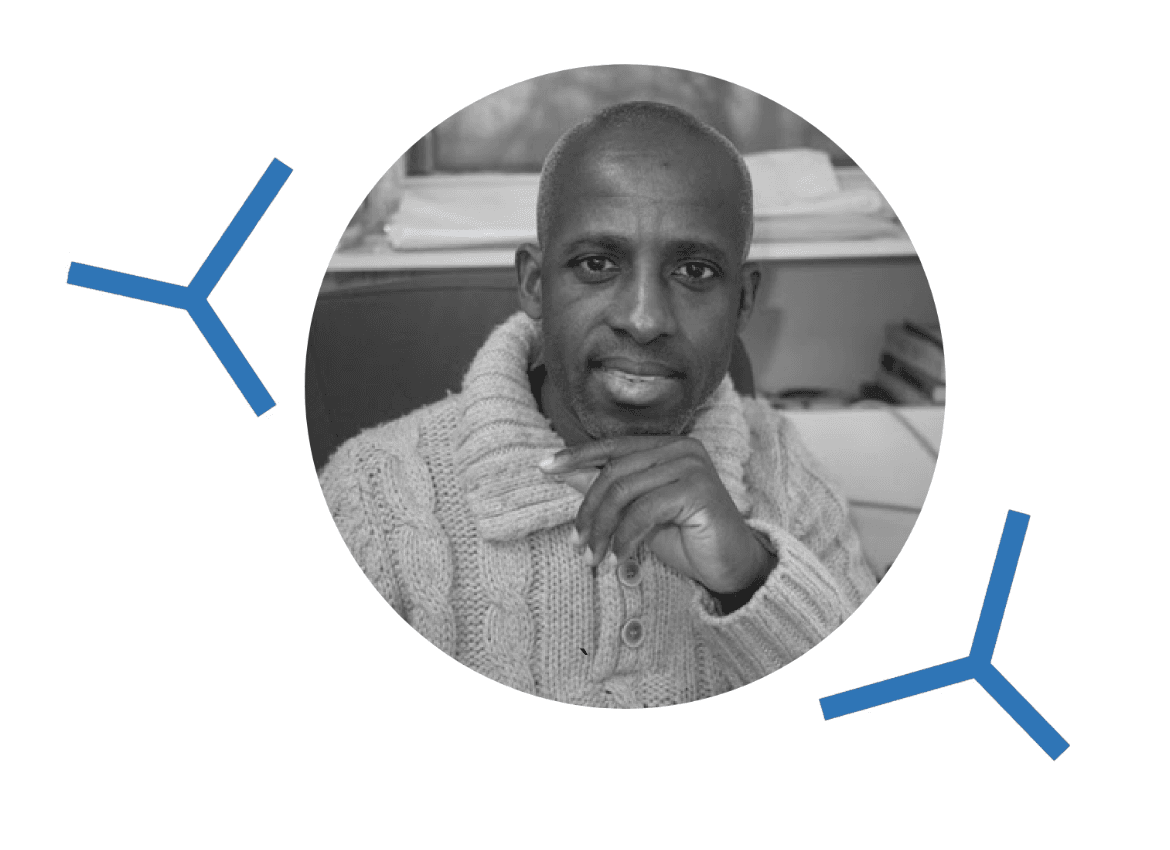
Guy Dirras, the project leader, is currently the Vice-President in charge of international relations at the University of Sorbonne Paris Nord, a professor at the IUT of Saint-Denis – Department of Science and Materials Engineering, and a researcher at LSPM, UPR-CNRS 3407. He is also the director of the joint laboratory (LabCom) CNRS-Z3DLAB « OPTIMAA. » He has authored over 120 publications and is involved in several collaborative research programs, both public/private and international partnerships, in various scientific leadership roles. These programs include ANR projects such as “SHIELD,” “CoCoA-Bio,” “TurboAhead,” “HighS-Ti,” “MAUDE”; DGA’s PEA programs “AHE” and RAPID’s “MADRYD”; and the FUI program “PALOMA.”
His scientific interests are interdisciplinary, aiming to identify microstructural phenomena and the elementary mechanisms of plasticity that govern the macroscopic mechanical behavior of metals and alloys, including high-entropy alloys (HEA). His traditional research areas include powder metallurgy, the study of mechanical behavior, and the analysis of deformation and fracture mechanisms, particularly the interactions between structural defects (dislocations, precipitates, grain boundaries, etc.). His current research focuses on microstructure engineering (high-entropy refractory alloys, harmonic structures based on titanium, gradient microstructures in metals and alloys), coupled with the identification of deformation mechanisms under stress, and the development of new material solutions for biomedical implants.
He is supported by a team of permanent staff, including researchers, faculty members, engineers, and technicians: A. Hocini (IR, mechanical testing, and post-treatment CIC), M. Konstantakopoulou (IE, Microscopy), P. Langlois (CR, powder metallurgy), and D. Tingaud (MCF, material processes and chemistry).
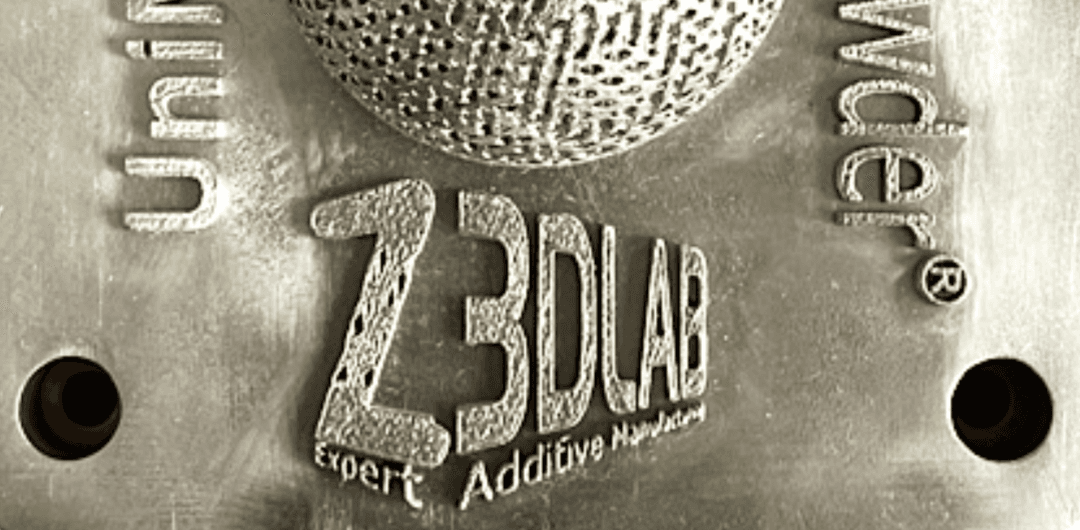